Welding is a skilled trade because it requires technical skills and the use of complicated welding equipment. And regardless of whether you’re a new welder pursuing the field, or a seasoned one, your success depends largely on how well you can use these implements. That’s why it’s important to understand how to use welding equipment optimally.
In this blog post, we bring you 19 essential pieces of welding equipment that you should have in you as a master welder. But first things first, let’s define the role and duties of welders.
What is a Welder?
A welder is a skilled professional who “fuses” materials together through the use of high heat. Fusing in this sense essentially refers to the joining of two materials together. In welding, the materials are heated and melted, causing them to remain fused when cooled. This process is often used in operations concerning the construction, automotive, aerospace, shipping, and manufacturing industries. Furthermore, this process is also useful for fabricating materials. Because, practically speaking, welding is an altogether important process in many industries.
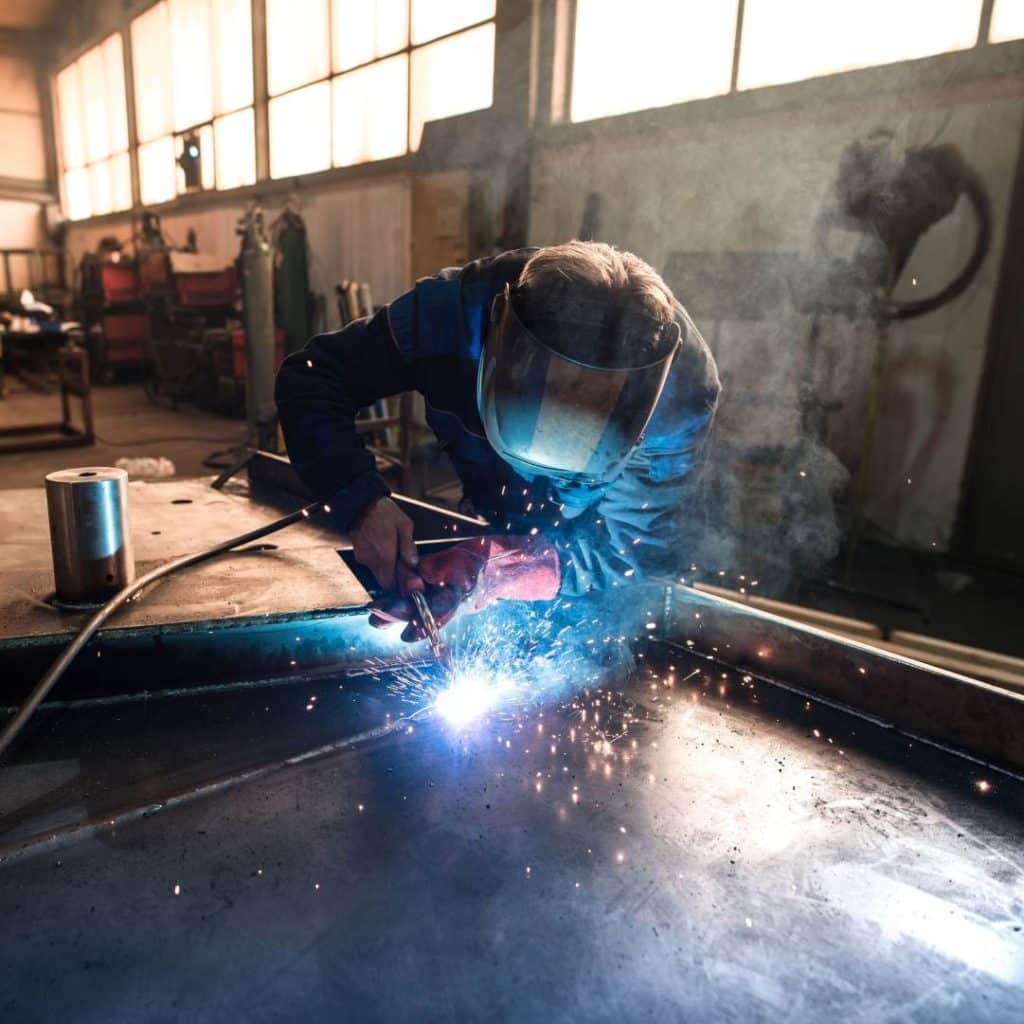
What is Welding?
Before we dive into the tools, let’s first understand what welding is all about. Welding is the art of joining materials together using high heat, creating a strong bond that can withstand the test of time. It’s a vital skill used across various industries, from construction as well as manufacturing.
Numerous Types of Welding Processes
There are also numerous types of welding processes facilitated by general contractors. In the Philippines, the most common welding processes are the following:
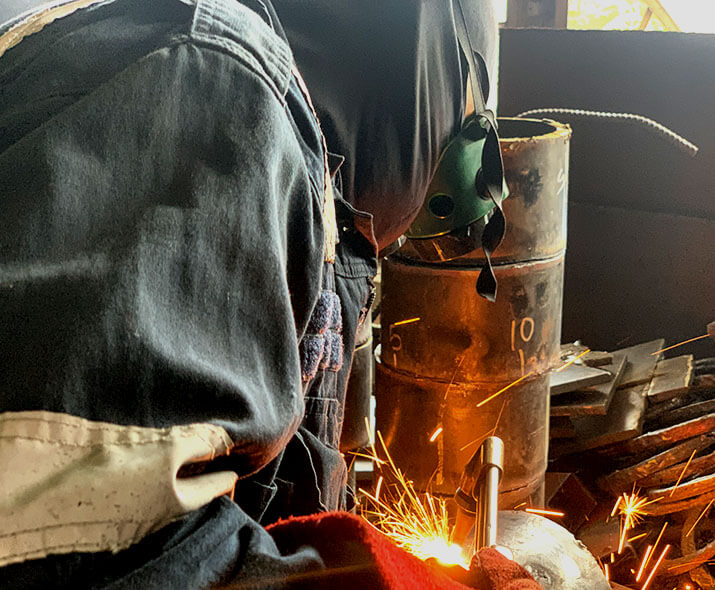
Gas Metal Arc Welding (GMAW)
Also known as MIG (Metal Inert Gas) welding, GMAW uses a wire electrode that’s fed through a welding gun. The arc is created between the wire electrode and the workpiece, melting them together. A shielding gas is used to protect the weld from atmospheric contamination. Additionally, GMAW is versatile and can be used on a variety of metals and thicknesses. It’s commonly used in industries like automotive, construction, and manufacturing.
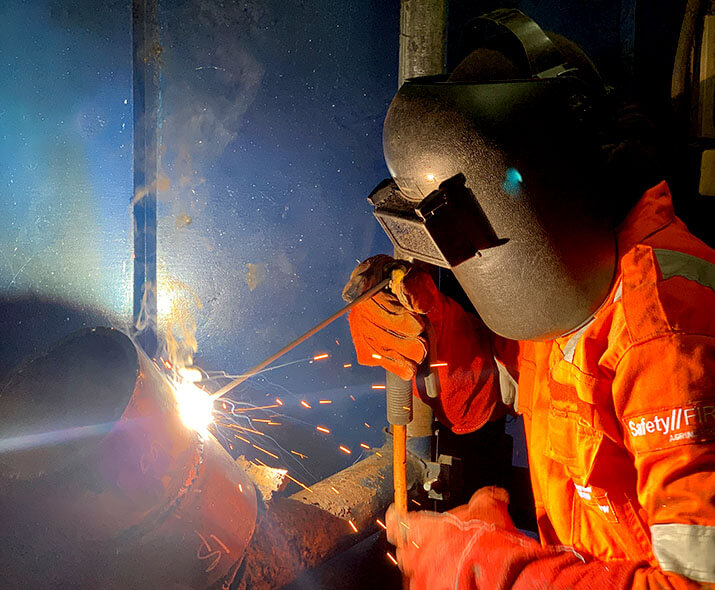
Shielded Metal Arc Welding (SMAW)
SMAW, often called stick welding, uses a flux-coated electrode. The arc is formed between the electrode and the workpiece, creating the weld as the electrode melts. The flux coating essentially provides a shielding gas and forms a slag layer to protect the weld. SMAW is portable and can be used in outdoor or windy conditions, making it popular in construction and repair work. Furthermore, it’s versatile but can be slower compared to other methods.
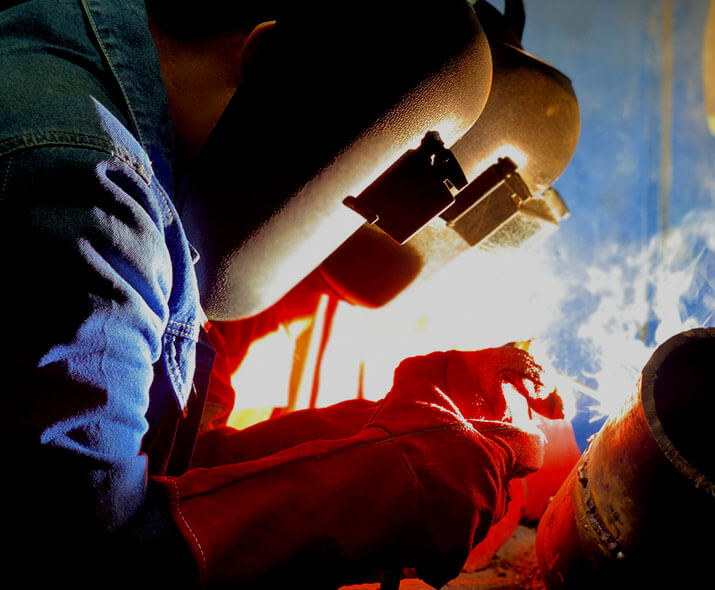
Gas Tungsten Arc Welding (GTAW)
Also known as TIG (Tungsten Inert Gas) welding, GTAW uses a non-consumable tungsten electrode to create the arc. A separate filler rod is often used to add material to the weld. Meanwhile, a shielding gas protects the weld. GTAW produces high-quality welds and is used for precise work on thin materials or exotic metals like stainless steel, aluminum, and copper. It’s common in industries like aerospace, automotive, and precision fabrication.
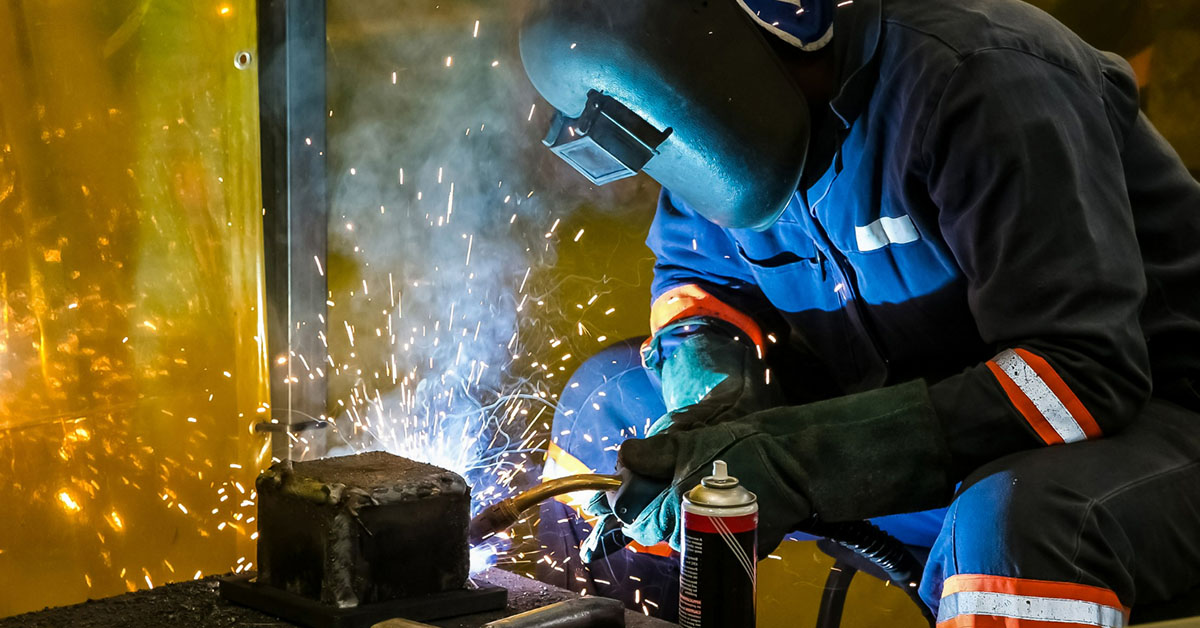
Flux-Cored Arc Welding (FCAW)
FCAW is similar to GMAW but uses a tubular wire filled with flux instead of a solid wire. The flux significantly generates a shielding gas when it melts, protecting the weld. It can be used with or without shielding gas from an external source. Moreover, FCAW is often used for welding thicker materials outdoors or in windy conditions, where gas shielding might be less effective. It’s common in construction, shipbuilding, and heavy equipment fabrication.
.
Responsibilities of a Welder
Primarily, a welder’s responsibility is to fuse two pieces of materials using welding machines, which are meant to apply heat to metal, plastic, or wood materials. Other duties of a welder may vary depending on the industry they are under, but generally speaking, welders are responsible for the following:
-
- Reviewing technical drawings and blueprints
- Examining materials for dimensions and flaws
- Initiating and controlling welding torches
- Monitoring the welding process for safety and quality
- Maintaining tools and equipment
The 19 Most Important Welding Equipment And Other Tools of Trade
Now that we have gone over the basics of welding, let’s dive into the 19 essential welding equipment and accessories that welders use to perform their duties.
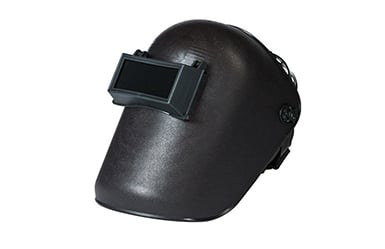
1. Welding Helmet
Safety is paramount in welding, and a quality welding helmet is a must-have for protecting your face and eyes from sparks and UV radiation.
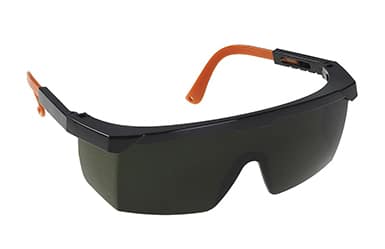
2. Safety Glasses
In addition to a welding helmet, safety glasses provide an extra layer of protection for your eyes against UV light and debris.
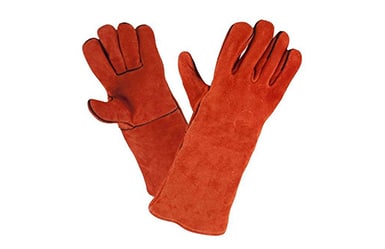
3. Welding Gloves
Protect your hands from heat and sparks with a pair of durable welding gloves. Look for gloves that offer both comfort and dexterity for maximum performance.
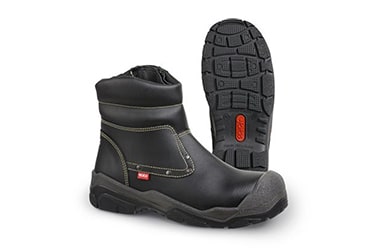
4. Welding Boots
Keep your feet safe from molten metal and other hazards with a sturdy pair of welding boots. Look for boots with steel reinforcement for added protection.
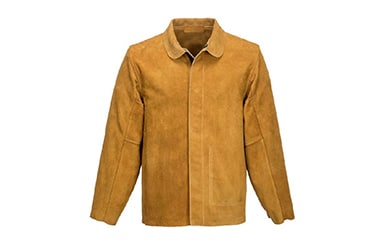
5. Welding Jacket
A welding jacket provides full-body protection against sparks and flames, making it an essential garment for any welder.
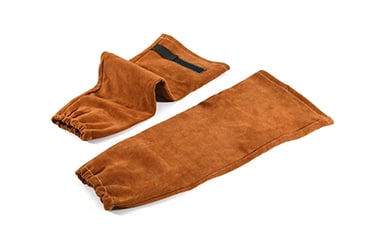
6. Welding Sleeves
For jobs that require greater mobility, welding sleeves offer protection for your arms without sacrificing comfort.
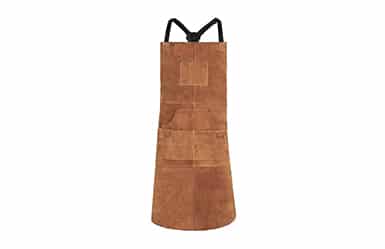
7. Welding Apron
An apron provides additional protection for your torso and legs, keeping you safe from sparks and heat.
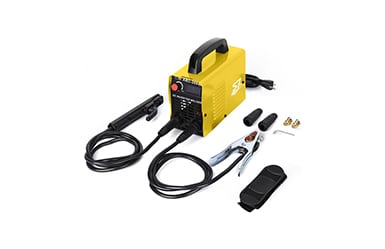
8. Welding Machine
At the heart of every welder’s toolkit is the welding machine. Because these devices provide the power and precision needed to fuse materials, making them an essential component of any welding setup.
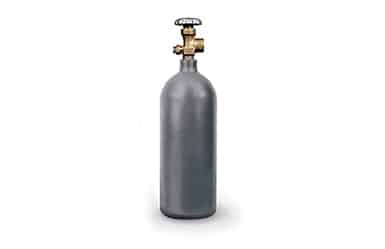
9. Shielding Gas and Cylinder
Shielding gases protect the welding area from atmospheric contaminants, ensuring clean and strong welds. Storing these gases in specialized cylinders makes them easy to use and refill as needed.
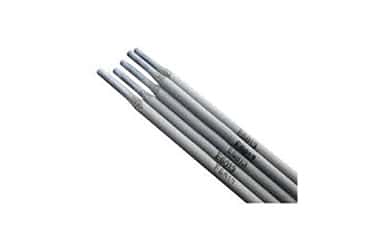
10. Consumable Electrodes
Electrodes are the lifeblood of arc welding because they produce the heat and arc needed to create welds. Choosing the right electrode for the job is crucial for achieving optimal results.
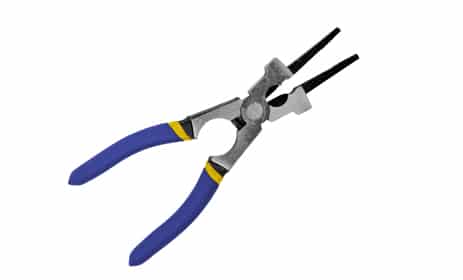
11. MIG Pliers
MIG pliers are versatile tools that can be used for various tasks, from removing nozzles to clipping wires.

12. Welding Magnets
Hold your workpieces securely in place with strong welding magnets, available in various sizes and strengths.

13. C Clamps
Secure your materials to a work surface with sturdy C clamps, preventing warping and distortion during welding.
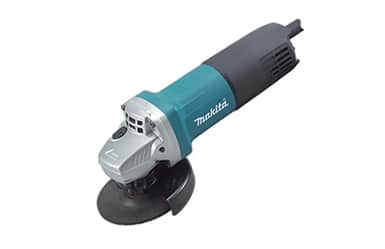
14. Angle Grinder
An angle grinder is a versatile welding equipment meant for cutting, grinding, and polishing metal, making it indispensable in any welder’s toolkit.
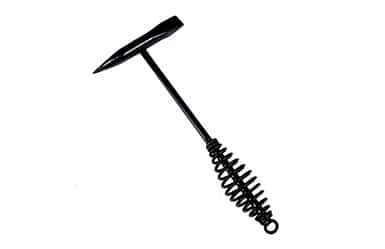
15. Chipping Hammer
This type of welding equipment is used to remove slag and debris from your welds with a chipping hammer, ensuring a clean and professional finish.
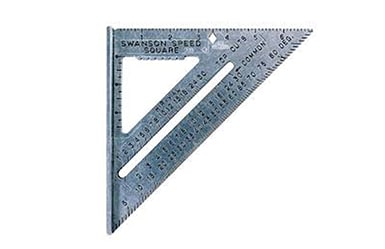
16. Speed Square
Measure and mark materials with precision using a speed square, essential for making accurate cuts and angles.
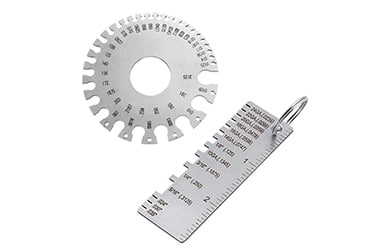
17. Sheet Metal Gauge
Ensure consistent welds with a sheet metal gauge, allowing you to measure metal thickness accurately.
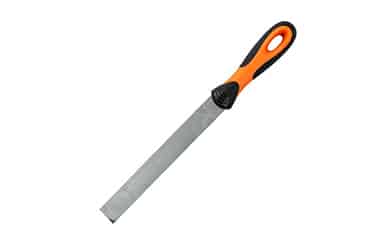
18. Metal File
Smooth rough edges and burrs with a metal file, perfect for fine-tuning your welds for a flawless finish.
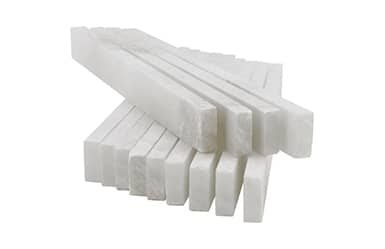
19. Soapstone
Mark your materials with ease using soapstone, a heat-resistant tool that’s essential for layout and design.
Want to Pursue a Career in Welding?
If you want to pursue a career in welding, you must first master the use of the welding tools in this list. We invite you to enroll in our welding training school! We offer comprehensive welding training programs, covering Gas Tungsten Arc Welding (GTAW), Gas Metal Arc Welding (GMAW), Shielded Metal Arc Welding (SMAW), and Flux Cored Arc Welding (FCAW).
You can also read our blog on how to kickstart your welding career by clicking on this link.
What is the difference between MIG, TIG, and stick welding equipment, and when is each used?
Well, MIG welding is fast and ideal for thin materials, TIG welding offers high precision for thick materials, and stick welding is versatile for outdoor and heavy-duty applications, particularly on dirty or rusty surfaces.
MIG is commonly used in industries like automotive, construction, and manufacturing due to its speed and ease of use. The TIG is often used used for precise work on thin materials or exotic metals like stainless steel, aluminum, and copper due to the high-quality welds it produces. Lastly, the stick welding is common in construction and repair work. It’s versatile but can be slower compared to other methods. Hope that this helps you a lot!
I was very pleased to find this web-site.I wanted to thanks for your time for this wonderful read!! I definitely enjoying every little bit of it and I have you bookmarked to check out new stuff you blog post.